When the flush of a new-born sun fell first on Eden's green and gold,
Our father Adam sat under the Tree and scratched with a stick in the mould;
And the first rude sketch that the world had seen was joy to his mighty heart,
Till the Devil whispered behind the leaves, "It's pretty, but is it Art?"
--From THE CONUNDRUM OF THE WORKSHOPS
by Rudyard Kipling
Visit my website: http://www.glassylady.com
Thursday, November 23, 2006
Cutting the Glass for Your Stained Glass Stepping Stone
Lay your individual pattern pieces on your stained glass. Either keep the pattern and glass with the right side up and facing you – or – put the pattern and the glass with the wrong side up and facing you. Be consistent. What you do with one, do with all. You might want to pay particular attention to any pattern or wave in the glass and lay your pieces out to capture that perfect swirl. For example, if you’re cutting out a flower, you may want the pattern in the petals to compliment each other or flow from one petal to another. The same goes for leaves. Don’t cut one piece with the pattern in the glass flowing across the leaf in an east-west direction and another with the flow of the glass going north-south. Of course, you may want that effect with certain patterns. Just be aware of these considerations as you lay your pattern out.
If you’d like, use a little spray adhesive or a touch of a glue stick to hold your pattern in place. Draw around the pieces and copy the piece number on to the glass with your marking pen. I try to remember to write the number on the side of the glass that will be facing up when the stone in complete. It makes cleaning it off later much easier.
Using your glass cutter, cut out all the shapes. Grind any sharp edges or go over them gently with a grozing stone. Work very carefully and watch out for those sharp edges! Clean the marking pen off the edges of the glass, but keep the numbers there for now.
Saturday, October 28, 2006
Printing and Cutting Your Pattern for Your Stained Glass Stepping Stone
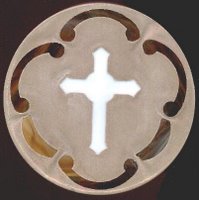
Once you’ve chosen your pattern, print it twice: once onto a heavier stock of paper and once on regular paper. Assign a number to each piece in the pattern and write it on both copies. This assumes you’re using your computer printer. If you’re using a photocopier, you can write the numbers in first and then copy.
On the light weight copy, we will make a template in the shape of the mold. Stepping stone, trivet and coaster molds are available at craft stores or from stained glass suppliers, as well as online. They come in a variety of materials – heavy duty to light weight. Another very handy and inexpensive source for a stepping stone mold is the large, clear, lightweight plastic flowerpot saucer. These are available at any garden center. They are flexible and make removing your stone a piece of cake. Just make sure they are smooth bottomed without any pattern (unless you want that pattern on the top of your stone). To make the template, place the mold on the paper, making certain your pattern is centered, and draw the outline of the mold. You now have a “frame” around your pattern. Cut around this outline/frame and place it into your mold, making sure it fits neatly against all the edges. There’s a reason for this which will be explained later. Once you’ve got everything trimmed up correctly, remove this template from the mold form and set both aside.
Cut out your pattern on the heavier stock following the heavy black lines. If you have pattern scissors, use those. They will cut a channel between all the pieces in the pattern. If you don’t have a pair of these, use regular scissors and be sure to trim away all the black. Why? When making a stained glass panel, you join all the pieces together with came lead or copperfoil and solder. The channel cut between the pattern pieces allows for this added material. If you sew, think of it as the seam allowance. With stepping stones, you want the concrete to flow in between the pieces and act as the lead.
Stay tuned for more...
Monday, October 23, 2006
Making Stained Glass Stepping Stones - It All Starts with an Idea
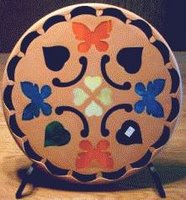
And it’s called a pattern. It may be something you come up with in your own creative head. It may be a pattern designed by someone else and published in a book. It may even be a picture from a child’s coloring book (big pictures, thick lines)! Check out the pattern in that beautiful quilt that grandma made 40 years ago. Quilt patterns make beautiful stepping stones.
If the source of your pattern is something other than your own brain, be aware of copyright restrictions. These are usually stated in the front of the book. Some designers will only allow you to use their patterns to make stones for your own enjoyment or gift-giving. Some will allow you to sell what you make, but will restrict the number you can sell. Often, the author will ask you to call or write for permission. It’s easy to do the right thing and be legal while doing it.
There are also many resources on the internet for free patterns. Here’s a partial list to get you started.
Chantal's Stained Glass
Craft Patterns and Supplies, currently offering 4 free patterns if you do the printing from your computer.
Down East Stained Glass
http://stainedglasspatterns.com/
Craft Freebies - this is a fabulous source!
Friday, October 20, 2006
Tools of the Trade to Create Stained Glass Stepping Stones
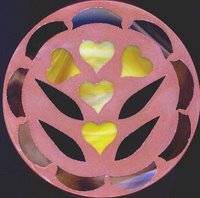
Tools and accessories you use for stepping stone construction should be strictly designated for stepping stone work. Do not use any of the following items later (even after washing) for food preparation, food serving or food storage. Keep all items separate and for use only with your concrete.
You will need
•Two large mixing buckets. 10 gallon plastic paint containers are more than adequate and are what I use when mixing for a large stone. Other favorites come from the local bakery where the containers have held the likes of corn syrup or baking mix. Sometimes these buckets are free. Sometimes the bakeries sell them for a dollar or two. Of course, there’s nothing wrong with a trip to the hardware store for a traditional metal bucket. They work too!
•Medium sized mixing buckets. 5 gallon size containers are handy for mixing trivets.
•A smaller container. Got margarine? A three pound plastic container is perfect for mixing trivets
•Measuring cups. Two sets, metal or plastic. Both will work. One set is used for dry measuring, one set for water.
•Measuring spoons. Again, metal or plastic.
•A paint stir. If you’ve ever purchased paint, you’ve probably got a few million of these lying around. Wood or plastic. It’s all good. And free.
•Rubber gloves. Cement mix is extremely abrasive and tough on the hands.
•Dust Mask
•Safety Glasses
•A glass cutter, if you plan to cut your own glass shapes.
•Running and/or breaking pliers, if you plan to cut your own glass shapes.
•Sandblasting resist or heavy contact paper (I prefer clear).
•Petroleum jelly
•Scissors, pattern scissors, or an exacto knife
•Marking pen
•Spray adhesive or glue stick
•Paper
•A pattern
•Mold (the plastic type, not the penicillin type)
•Assorted stained glass
•Newspaper
•Level
•DiamondCRETE
•6 – 8 Pencils
Optional items
Handy if you have them, but not required:
• Glass Grinder
• Mosaic Cutter
• Reflective Tape (which might be optional depending on the type of glass you use.
• Grozing Stone (cheaper than a grinder and you can use it to abrade any edges that need it.
Some folks like to have an electric drill with a paint stir attached. I personally don’t recommend it. It adds far too many bubbles to the mix and unless you come up with a way to get all of them out before your concrete mix sets up, you risk a stone that is riddled with tiny air bubbles and is thereby weakened. Use those rubber gloves and get in there with your hands. You can then feel for clumps or areas that need more blending and mixing.
Stay tuned for the next installment!
Tuesday, October 17, 2006
Brands of Glass for Your Stepping Stones
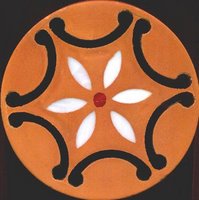
Brands of Glass
These are the primary brands available, although you may not have access to all of them locally.
• Armstrong
• Bullseye
• CBS Dichroic
• English Muffle
• Chicago Art Glass
• Kokomo
• Optimum
• Oceana
• Spectrum (remember that coupon deal at Hobby Lobby)
• Uroboros
• Wissmach
• Youghiogheny
• Wasser
Also available are brands such as Pattern 80, Duncan Architectural, German New Antique, French New Antique, Lamberts, New Antique Mirror, Krosno, Saint-Just Antiques, as well as jewels, crystals, engravings, medallions, bevels in various lusters and clusters, and probably more.
Again, many of these brands will be carried at local retail stained glass specialty stores, but you’ll pay a premium for them. Some are positively gorgeous and worth every penny. But for starters, I’d still stick with Spectrum for all the reasons listed previously.
Opalescent glass works well and doesn’t need any special treatment when using it in a stepping stone. Since it is opaque, you won’t see concrete through the glass.
Cathedral glass, on the other hand, needs a special step. Venture Tape makes a product called BriteBak Reflective Tape. It comes in silver or gold and is extremely sticky. You can back your cathedral pieces with this tape to prevent concrete being seen through the glass and to produce a wonderful dimension to the glass. Read all about it here.
Sunday, October 15, 2006
Types of Glass and Your Stepping Stones
Cathedral glass, while colored or colorless, is transparent. In other words, you can see your hand through it. You can read a book through it, and you can see concrete through it. So, when using this type of glass in stepping stones, it is necessary, in my opinion, to back the glass with wide Venture Tape. More on that later.
Opalescent glass is more opaque. It comes as a solid color but also with several colors or shades mixed together to produce a beautiful pattern of waves and swirls.
Within each of these two categories are several sub-categories. In alphabetical order they are antique, Baroque, collage, crackle, dichroic, drapery, Flemish, foxtail, globs, glue chip, fibroid, granite textured, hammered, honeycomb, iridized, noogie, pinnacle, ring mottle, ripple, rondels, rough cast, rough rolled, seedy, slush, machine rolled smooth, smooth ripple, stipple, streakies, trapunto, wispy, and more. Some of these terms are used exclusively by one company or another, but the majority are fairly common to most.
When making stained glass stepping stones, smooth glass is preferred. I find Spectrum brand to be good for many reasons.
• It has a nice smooth texture which is particularly suited to stepping stones.
• It is reasonably priced.
• It cuts easily.
• There is a wide variety of pretty colors and types available.
• It’s made in the USA.
• It is easily accessible because it’s the brand that Hobby Lobby carries.
Unless you’ve got a wholesale account with a stained glass supplier, craft stores are a great source for manageable amounts of glass that won’t break the bank. Go to Hobby Lobby's website and sign up for a weekly email notification of their internet coupons. Or, if you prefer, click here to see what’s offered for the week. Sometimes, the week’s special is 50% off stained glass. Just print that coupon and take it to Hobby Lobby for a great deal. Buy one piece or buy 100. There’s no limit. Other times, a coupon for 40% off one item is offered. Also not a bad deal.
Next up: Brands of Glass for Your Stepping Stones
Saturday, October 14, 2006
Work Space for Creating Stained Glass Stepping Stones
Choose an area that is well ventilated. While it is fine to have a fan going while you cut glass or arrange pattern pieces, you will need to turn it off while pouring the dry concrete mixture into your mixing container. The dust is superfine, and moving air will stir it up even more. Wear a dust mask.
The Table
Table height is an individual thing based on your height. If you’re using a workbench or a regular table, the height will be predetermined for you. But if you’re tall, you might want a higher surface. Just remember that you’ll be standing most of the time (I’ve never been able to cut glass while sitting in a chair or on a stool). And you’ll be bending over when you pour. At least I find it necessary to work in these positions. Men’s center of gravity is in their shoulders or upper body, and they can pour a bucket of cement into a mold on a table much easier than a woman. Women’s center of gravity is in their hips, so pouring is more of a challenge. At least it is for me. With time, you will find what works best for you. But in the meantime, save your back and find a comfortable height for your work surface.
Indoors or Out?
The majority of us will probably be working indoors most of the time. When it comes time to pour the concrete, I always move to an area of the basement where I can clean up easily, or to the garage where a little spill would not be a catastrophe, or outdoors when the weather is nice. Of course, the great outdoors may be where you conduct most of this stepping stone business anyway, in which case, avoid windy days.
Work Safely While Making Your Stained Glass Stepping Stones
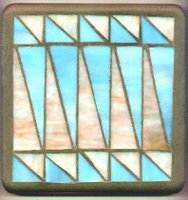
This may seem obvious, but it is absolutely crucial that you wear shoes while working with glass. Not sandals, not slippers, not open-toed fashion statements, and certainly not unprotected bare feet, but real, honest-to-goodness sturdy shoes which enclose your entire foot. You might even consider steel-toed boots.
I speak from experience, my friends. One day, while trying to salvage glass from a stepping stone damaged by a clumsy customer, a hairline crack grew into something much bigger. Half of an 18” concrete stepping stone fell off my work table and onto my sandaled foot. Not pretty. It took a full year and then some for my toenail to reach its previously healthy and attractive state. Naturally, I was working alone, but I managed to crawl to my bed and elevate my foot on the headboard without passing out. But it was close.
I made two mistakes. The first was not wearing a real shoe. The second was trying to salvage this stone. Take it from one who’s been there. If your stone is dropped and/or cracks for some reason, don’t try to save any of it. Take it straight to the dumpster and move on.
My point is simply this. Use common sense, be extra careful, and have a healthy respect for the damage that concrete and sharp glass can do to the human body. Keep young ones at a safe distance and insist that they also wear shoes if they are watching or helping. Tiny little pieces of glass that you may not see might end up embedded in the bottom of a foot. A nice crunch is a better sound than screams of agony. Stitches are no picnic for the injured party or the family member or friend who is there to watch the doctors work.
So, be safe and keep focused on the work before you, and you will hopefully avoid serious injury.
Friday, October 13, 2006
How to Make a Stained Glass Stepping Stone

After receiving hundreds of requests for information and instructions on how to make garden stepping stones inlaid with stained glass, I decided to make this blog in order to explain the steps I take and the tricks I use to produce consistently successful results as seen here.
This blog is not meant to be an exhaustive resource, but rather it contains the secrets to my success. Included in future posts will be the brand names of the products I use, contact information for the companies which manufacture the materials needed, mail order sources, national retail suppliers which may be available to you locally, and techniques to help you make a beautiful stepping stone on the first try. I'll try to add a little bit each day, so keep checking back.
Upcoming topics:
- Tools and Materials List
- Instructions
- Sources for supplies
- Installation instructions
- Internet resources
Tuesday, October 10, 2006
Stained Glass is My Passion
I get quite a number of requests to share some of my trade secrets. While I'm not inclined to share all of them, I have decided to make this blog a place where I can talk about stained glass and share a few techniques that I've used over the years. My first topic will be making stained glass stepping stones. Stay tuned!